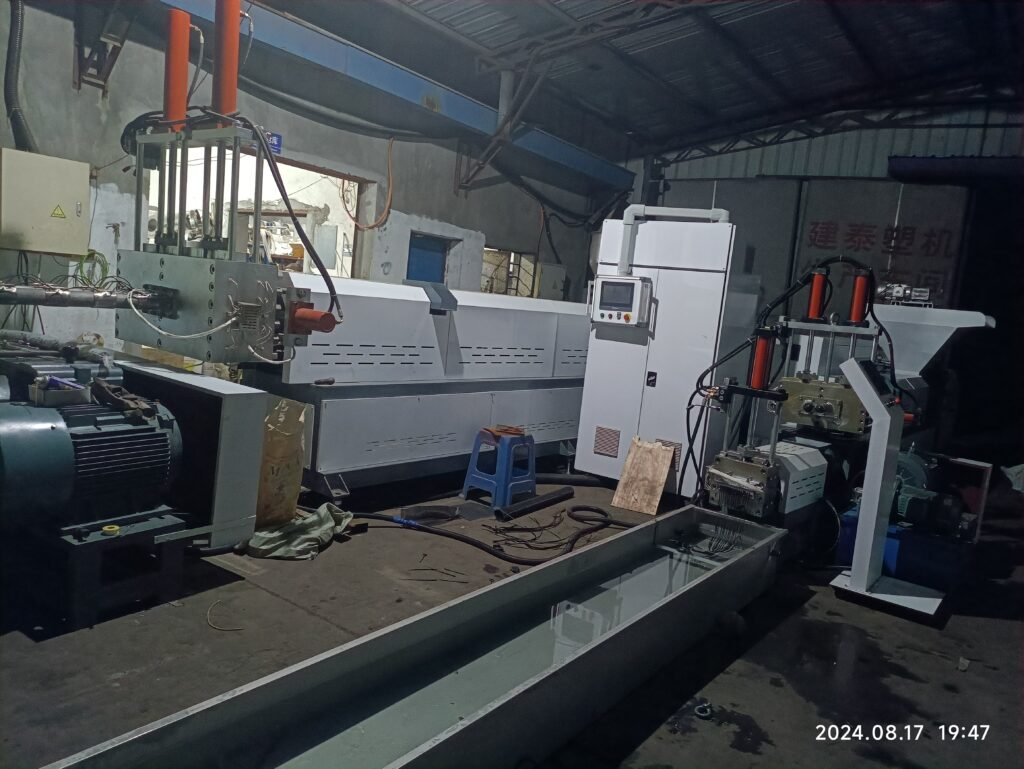
Introduction
PVC (Polyvinyl Chloride) plastic machinery plays a crucial role in the plastics industry, enabling the transformation of PVC resin into a wide variety of products. From pipes and profiles to sheets and films, PVC plastic machinery is designed to handle the unique properties of PVC and produce high-quality, durable products. In this blog post, we will explore the principle, process, processing, maintenance, and after-sales service of PVC plastic machinery.
Principle of PVC Plastic Machinery
The working principle of PVC plastic machinery varies depending on the type of machine and the specific process it is designed to perform. However, most PVC plastic machinery operates based on the following fundamental principles:
Extrusion
Extrusion is one of the most common processes used in PVC plastic machinery. In extrusion, PVC resin is melted and forced through a die to form a continuous shape, such as a pipe, profile, or sheet. The extrusion process involves several key components, including a hopper, a screw conveyor, a heating barrel, a die, and a cooling system.
The hopper is used to feed the PVC resin into the machine. The screw conveyor then transports the resin through the heating barrel, where it is melted by the heat generated by the barrel and the friction of the screw. The melted resin is then forced through the die, which gives it the desired shape. The cooled product is then pulled away from the die by a haul-off unit and cut to the desired length.
Injection Molding
Injection molding is another widely used process in PVC plastic machinery. In injection molding, PVC resin is melted and injected into a mold cavity under high pressure. The mold cavity is designed to shape the melted resin into the desired product. Once the resin has cooled and solidified, the mold is opened, and the finished product is ejected.
The injection molding process involves several key components, including an injection unit, a clamping unit, a mold, and a cooling system. The injection unit is used to melt the PVC resin and inject it into the mold cavity. The clamping unit is used to hold the mold closed during the injection process and to open the mold when the product is ready to be ejected. The mold is designed to shape the melted resin into the desired product. The cooling system is used to cool the product and to help it solidify quickly.
Blow Molding
Blow molding is a process used to produce hollow PVC products, such as bottles and containers. In blow molding, PVC resin is melted and formed into a parison, which is a tube-like shape. The parison is then placed in a mold cavity and inflated with air or another gas to conform to the shape of the mold. Once the product has cooled and solidified, the mold is opened, and the finished product is ejected.
The blow molding process involves several key components, including an extruder, a parison former, a mold, and a blowing unit. The extruder is used to melt the PVC resin and to form it into a parison. The parison former is used to shape the parison into the desired shape. The mold is designed to shape the inflated parison into the desired product. The blowing unit is used to inflate the parison with air or another gas.
Process of PVC Plastic Machinery
The process of PVC plastic machinery can be divided into several stages, including raw material preparation, processing, and finishing.
Raw Material Preparation
The first stage in the process of PVC plastic machinery is raw material preparation. This involves selecting the appropriate PVC resin and additives for the desired product. PVC resin is available in a variety of grades and formulations, each with its own unique properties. Additives, such as plasticizers, stabilizers, fillers, and colorants, are added to the PVC resin to modify its properties and to enhance its performance.
Once the raw materials have been selected, they are typically mixed together in a mixer to ensure a uniform distribution of the additives. The mixed raw materials are then fed into the PVC plastic machinery for processing.
Processing
The processing stage is the heart of the PVC plastic machinery process. This is where the PVC resin is transformed into the desired product using one of the processes described above, such as extrusion, injection molding, or blow molding.
During the processing stage, the PVC resin is melted and shaped into the desired form. The temperature, pressure, and speed of the machine are carefully controlled to ensure that the product is of the highest quality. The processed product is then cooled and solidified before being removed from the machine.
Finishing
The final stage in the process of PVC plastic machinery is finishing. This involves further processing the product to improve its appearance, performance, or functionality. Finishing operations may include cutting, trimming, drilling, sanding, painting, or printing.
The specific finishing operations required will depend on the type of product being produced and the desired end-use. For example, PVC pipes may be cut to length and threaded, while PVC sheets may be trimmed and laminated. PVC products may also be decorated with labels, logos, or other graphics to enhance their visual appeal.
Processing of PVC Plastic Machinery
The processing of PVC plastic machinery requires careful attention to detail and the use of proper techniques to ensure the production of high-quality products. Here are some key factors to consider when processing PVC with plastic machinery:
Temperature Control
Temperature is a critical factor in the processing of PVC plastic machinery. PVC resin has a relatively narrow processing temperature range, and if the temperature is too high or too low, it can lead to a variety of problems, such as poor product quality, excessive wear on the machine, or even machine failure.
To ensure proper temperature control, it is important to use a reliable heating and cooling system and to monitor the temperature of the machine and the product closely. The temperature of the heating barrel, die, and other components should be set according to the specific requirements of the PVC resin and the product being produced.
Pressure Control
Pressure is another important factor in the processing of PVC plastic machinery. The pressure applied to the PVC resin during the extrusion, injection molding, or blow molding process can affect the quality and consistency of the product. If the pressure is too high, it can cause the product to be over-pressurized and may lead to defects such as warping, cracking, or porosity. If the pressure is too low, it can result in a product that is under-filled or has poor surface finish.
To ensure proper pressure control, it is important to use a reliable pressure gauge and to adjust the pressure according to the specific requirements of the PVC resin and the product being produced. The pressure of the screw conveyor, injection unit, or blowing unit should be set to the appropriate level to ensure that the PVC resin is processed evenly and consistently.
Screw Design
The screw design of the PVC plastic machinery can also have a significant impact on the processing of PVC resin. The screw is responsible for transporting the PVC resin through the heating barrel, melting it, and forcing it through the die. The design of the screw, including the pitch, diameter, and length, can affect the melting efficiency, mixing ability, and pressure generation of the machine.
To ensure optimal screw design, it is important to select a screw that is appropriate for the specific requirements of the PVC resin and the product being produced. The screw should be designed to provide efficient melting and mixing of the PVC resin while minimizing shear stress and degradation. The length and diameter of the screw should also be selected to ensure that the PVC resin is processed evenly and consistently.
Die Design
The die design of the PVC plastic machinery is another critical factor in the processing of PVC resin. The die is responsible for shaping the melted PVC resin into the desired product. The design of the die, including the shape, size, and internal geometry, can affect the quality and consistency of the product.
To ensure optimal die design, it is important to select a die that is appropriate for the specific requirements of the PVC resin and the product being produced. The die should be designed to provide a smooth and uniform flow of the melted PVC resin while minimizing turbulence and pressure drop. The shape and size of the die should also be selected to ensure that the product is of the desired dimensions and has the required surface finish.
Maintenance of PVC Plastic Machinery
Proper maintenance of PVC plastic machinery is essential to ensure its long-term performance, reliability, and safety. Regular maintenance can help to prevent breakdowns, reduce downtime, and extend the lifespan of the machine. Here are some key maintenance tasks that should be performed on PVC plastic machinery:
Cleaning
Regular cleaning of the PVC plastic machinery is essential to remove dirt, dust, and other contaminants that can accumulate on the machine over time. Cleaning can help to prevent wear and tear on the machine, improve its performance, and reduce the risk of contamination of the product.
The machine should be cleaned regularly using a suitable cleaning agent and equipment. The heating barrel, die, screw, and other components should be cleaned thoroughly to remove any residue or buildup of PVC resin. The cooling system should also be cleaned regularly to ensure proper cooling of the machine and the product.
Lubrication
Lubrication is another important maintenance task that should be performed on PVC plastic machinery. Proper lubrication can help to reduce friction and wear on the machine, improve its performance, and extend its lifespan.
The machine should be lubricated regularly using a suitable lubricant and equipment. The bearings, gears, screws, and other moving parts should be lubricated according to the manufacturer’s recommendations. The lubricant should be selected based on the specific requirements of the machine and the operating conditions.
Inspection
Regular inspection of the PVC plastic machinery is essential to identify any potential problems or issues before they become major problems. Inspection can help to prevent breakdowns, reduce downtime, and extend the lifespan of the machine.
The machine should be inspected regularly by a qualified technician. The inspection should include a visual inspection of the machine, as well as a check of the electrical, mechanical, and hydraulic systems. The technician should also check the temperature, pressure, and other operating parameters of the machine to ensure that they are within the normal range.
Replacement of Wear Parts
Over time, the wear parts of the PVC plastic machinery, such as the screws, dies, bearings, and seals, will need to be replaced. Replacement of wear parts is essential to ensure the continued performance and reliability of the machine.
The wear parts should be replaced according to the manufacturer’s recommendations. The replacement parts should be of high quality and should be compatible with the machine. The technician should also ensure that the replacement parts are installed correctly and that the machine is properly adjusted after the replacement.
After-Sales Service of PVC Plastic Machinery
After-sales service is an important aspect of the PVC plastic machinery industry. A reliable after-sales service provider can help to ensure the long-term performance, reliability, and safety of the machine. Here are some key services that should be provided by an after-sales service provider:
Technical Support
Technical support is essential to help customers solve any problems or issues they may encounter with their PVC plastic machinery. The after-sales service provider should have a team of qualified technicians who are available to provide technical support by phone, email, or on-site.
The technician should be able to diagnose the problem quickly and provide a solution. They should also be able to provide advice on how to prevent similar problems in the future. The after-sales service provider should also offer training to customers on how to operate and maintain their PVC plastic machinery.
Spare Parts Supply
The after-sales service provider should be able to supply high-quality spare parts for the PVC plastic machinery. The spare parts should be of the same quality as the original parts and should be compatible with the machine. The after-sales service provider should also have a stock of commonly used spare parts to ensure that they are available when needed.
The after-sales service provider should be able to deliver the spare parts quickly and efficiently. They should also provide advice on how to install the spare parts correctly and how to test the machine after the installation.
Maintenance and Repair Services
The after-sales service provider should offer maintenance and repair services for the PVC plastic machinery. The maintenance services should include regular cleaning, lubrication, inspection, and replacement of wear parts. The repair services should include the diagnosis and repair of any problems or issues that may occur with the machine.
The after-sales service provider should have a team of qualified technicians who are available to perform the maintenance and repair services. The technicians should be able to work quickly and efficiently to minimize downtime. The after-sales service provider should also offer a warranty on the maintenance and repair services.
Upgrades and Retrofits
The after-sales service provider should be able to offer upgrades and retrofits for the PVC plastic machinery. Upgrades and retrofits can help to improve the performance, reliability, and safety of the machine. The after-sales service provider should be able to provide advice on the best upgrades and retrofits for the specific requirements of the customer.
The upgrades and retrofits should be performed by qualified technicians. The technician should be able to install the upgrades and retrofits correctly and ensure that the machine is properly adjusted after the installation. The after-sales service provider should also offer a warranty on the upgrades and retrofits.
Conclusion
PVC plastic machinery is an essential part of the plastics industry, enabling the transformation of PVC resin into a wide variety of products. The principle, process, processing, maintenance, and after-sales service of PVC plastic machinery are all important factors to consider when selecting and using PVC plastic machinery. By understanding these factors, you can make informed decisions about the type of PVC plastic machinery that is best suited for your needs and ensure that it is operated and maintained properly to achieve the best possible results.