Introduction
PET extruder granulators are critical machines in the plastics recycling and manufacturing industries, converting post-consumer PET waste and virgin resin into high-value granules. This comprehensive guide explores the technical principles, operational processes, maintenance strategies, energy-saving innovations, compliance standards, and after-sales support for these sophisticated systems.
1. Core Working Principles of PET Extruder Granulators
PET granulation involves three interconnected stages:
1.1 Extrusion Mechanism
- Screw Design:
- Feeding Zone: Conveys solid material at 20-40% screw depth
- Compression Zone: Reduces volume by 3-5 times
- Metering Zone: Uniform melt viscosity at 250-280°C
- Barrel Configuration:
- 3-5 heating zones with PID temperature control
- Optional water-cooled feed throat
1.2 Melt Filtration
- Screen Pack System:
- 20-100 mesh filters remove contaminants
- Automatic backflush systems available
- Melt Pump:
- Maintains 50-150 bar pressure stability
- Ensures uniform die output
1.3 Granulation Process
- Strand Pelletizing:
- Melt extruded through die plate (1-4mm holes)
- Water bath cooling (15-25°C)
- Rotary cutter speed 100-300 RPM
- Underwater Pelletizing:
- Integrated water chamber cooling
- Direct pellet drying system
2. Complete Processing Workflow
2.1 Pre-Processing Stage
- Material Sorting:
- Near-infrared (NIR) sorting for contamination removal
- Moisture content <0.005% required
- Size Reduction:
- Shredders reduce flakes to 10-30mm
- Hammermills for fine grinding
2.2 Extrusion & Pelletizing
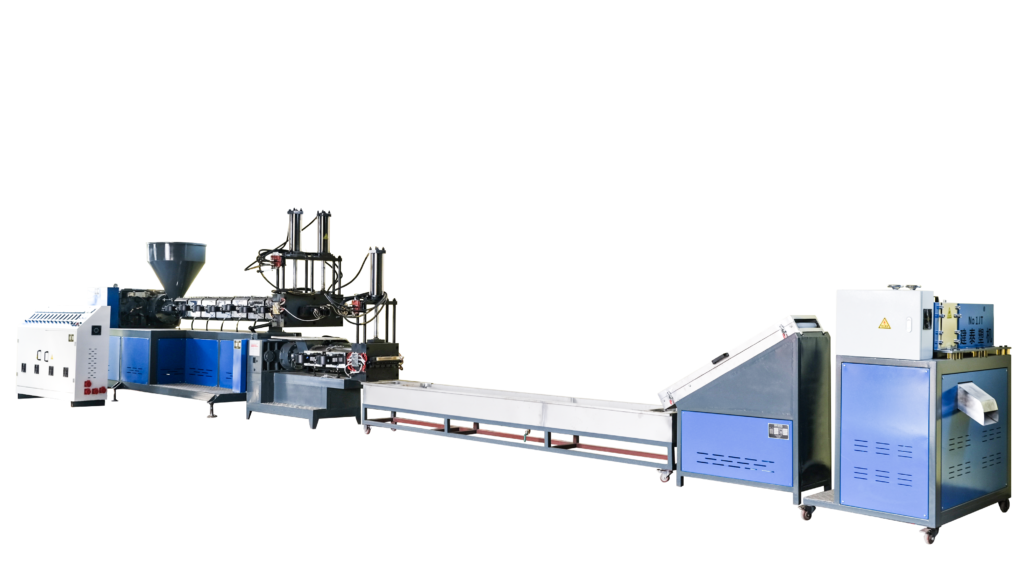
- Melting Profile:
- Zone 1: 220-240°C (solid conveying)
- Zone 2: 240-260°C (initial melting)
- Zone 3: 260-280°C (full melting)
- Die Plate Configuration:
- Hole diameter 1.5-3mm
- Hole density 100-300 holes/dm²
2.3 Post-Processing
- Drying:
- Fluidized bed dryer (50-70°C)
- Moisture content <0.1%
- Classification:
- Vibrating screens for size separation
- Magnetic separators for metal removal
3. Maintenance Strategies & Troubleshooting
3.1 Preventive Maintenance Schedule
Interval | Tasks |
---|---|
Daily | Check lubrication systems, clean die plate |
Weekly | Inspect screw wear, test temperature sensors |
Monthly | Replace filter screens, service gearbox |
Annual | Refurbish barrel, calibrate pressure transducers |
3.2 Common Issues & Solutions
- Problem: Uneven pellets
- Causes: Die blockage, cutter misalignment
- Solutions: Acid cleaning, laser alignment
- Problem: High melt temperature
- Causes: Screw speed too high, cooling failure
- Solutions: Reduce RPM, check chiller performance
- Problem: Low output
- Causes: Feeding system blockage, screen pack clogging
- Solutions: Clear hopper, increase backflush frequency
4. Energy-Saving Technology Applications
4.1 Case Study 1: Variable Frequency Drives (VFD)
- Implementation:
- VFDs installed on screw drive motors
- Power consumption reduced by 18-22%
- Cost Savings:
- Annual electricity savings of $12,000 for 100HP system
4.2 Case Study 2: Heat Recovery Systems
- Technology:
- Thermal oil loop captures barrel waste heat
- Preheats incoming material to 80-100°C
- Performance:
- Energy efficiency improved by 25%
- Payback period: 18-24 months
4.3 Case Study 3: High-Efficiency Motors
- Upgrade:
- IE5 motors replace standard IE3 models
- Efficiency increased from 92% to 96%
- Results:
- 4-6% energy reduction at full load
5. Industry Standards & Certifications
5.1 Key Regulatory Requirements
- ISO 9001: Quality management system
- ISO 14001: Environmental management
- FDA 21 CFR Part 177: Food contact compliance
- EU 10/2011: Migration limits for plastics
5.2 Certification Processes
- Material Testing:
- Melt flow index (250°C/2.16kg)
- Color stability (ΔE <1.5)
- Moisture content analysis
- Machine Validation:
- Pressure cycling tests
- Output consistency verification
- Safety interlock checks
6. Comprehensive After-Sales Support
6.1 Service Offerings
- Remote Monitoring:
- IoT-enabled predictive maintenance
- Real-time performance dashboards
- On-Site Services:
- Annual maintenance contracts
- Emergency breakdown response (48-hour SLA)
- Training Programs:
- Operator certification courses
- Process optimization workshops
6.2 Spare Parts Management
- Inventory System:
- Critical parts stocked locally
- 98% order fulfillment rate
- Customization:
- Die plates manufactured to order
- Screw designs optimized for specific materials
Future Innovations in PET Granulation
- AI Process Control:
- Machine learning for real-time parameter adjustment
- Closed-Loop Recycling:
- Integration with depolymerization systems
- Biobased PET Processing:
- Adaptations for plant-derived raw materials
Conclusion
PET extruder granulators are sophisticated systems requiring technical expertise in operation, maintenance, and optimization. By implementing advanced energy-saving technologies, adhering to international standards, and leveraging professional after-sales support, manufacturers can achieve sustainable production, cost efficiency, and compliance. As the industry evolves, these machines will continue to play a pivotal role in the circular economy of plastics.